Priemyselné roboty Motoman - zváranie, paletizácia, montáž, rezanie plazmou, laserom a vodou. Priemyselné roboty Motoman od Yaskawy sú zárukou japonského inžinierstva.
Welding, testing, handling in perfection by Gebr. Binder GmbH
Yaskawa robot cell convinces in high-volume production
Everything had to go quickly at Swabian Gebr. Binder GmbH Metallwarenfabrik. A large-scale order for the manufacture of about half a million sheet metal parts per year called for an extra-class production solution. Together with Yaskawa Europe, the company set out to create a production cell that would establish standards in terms of output, precision and availability.
- Priemyselné odvetvie
- Metalworking
- Zákazník
- Gebr. Binder GmbH
The Swabian automotive supplier Binder enjoys an excellent reputation in the industry. The family-owned company based in Neenstetten is considered reliable, customer-oriented and innovative, and supplies OEMs all over the world. With its approximately 800 employees, it is dedicated to forming technology and sheet metal processing. The fact that the fast expanding company was approached by a major German car manufacturer with an order for the series production of a sheet metal construction to accommodate the on-board batteries of certain vehicle series, speaks for the company’s reputation and performance.
Thomas Pflüger, mechanical engineer and Head of the Binder Production Joining and Welding Technology department: “Handling an order of this magnitude – the maximum production capacity is around half a million battery frames per year – would clearly not be possible without the investment in a completely new, highly automated system that integrates the necessary processes of spot welding, testing, signing and handling.”
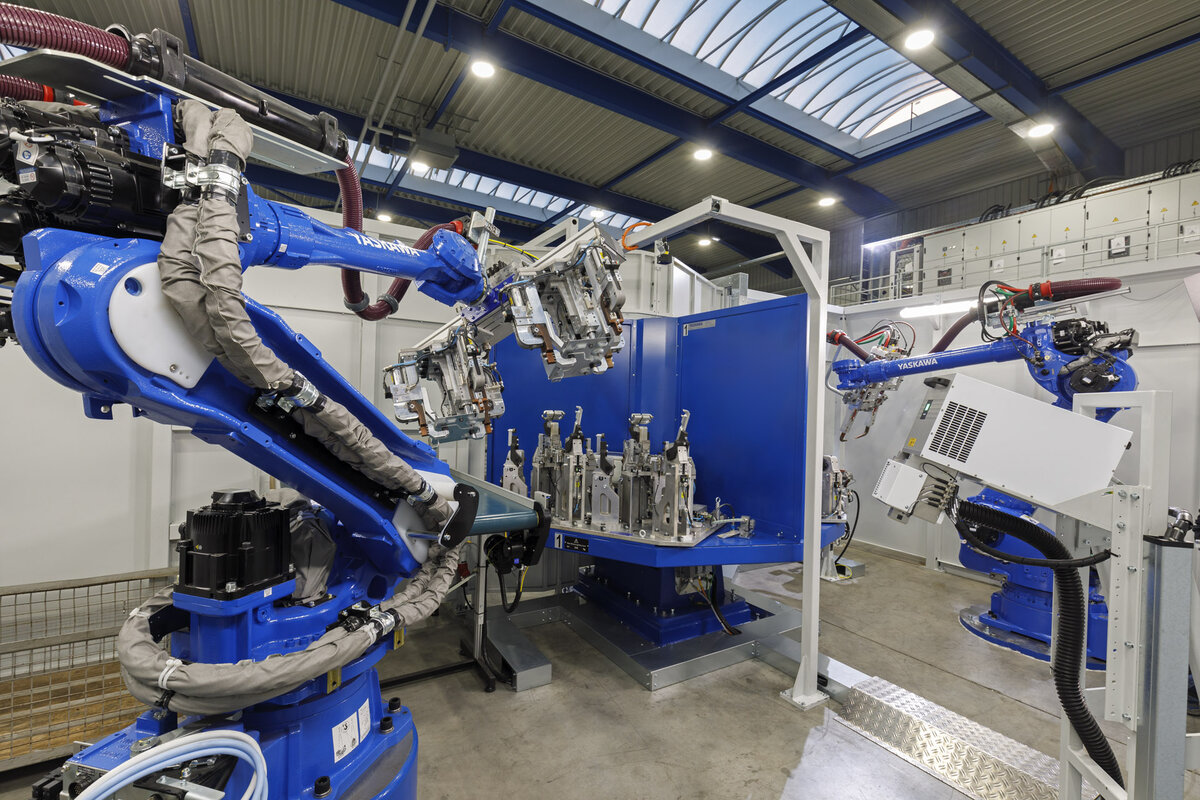
Picture: View into the cell: right the spot welding robot, in the foreground the laser signing station and left the GP88 six-axis robot for handling.
One operator, two robots, three stations
The Binder engineers immediately started working on a first rough draft, which conceptually outlined the essential stations of the new robot cell. This concept formed the basis for Yaskawa Europe, whose specialists were entrusted with the detailed planning and implementation of the complete system.
Roland Hermann, Senior Key Account Manager at Yaskawa, recalls: “We all knew that we could only achieve the cycle time specifications for this mass production part with the use of two six-axis robots, one for spot welding and another for overall handling. In addition, a three-station solution promised to be most viable, allowing all processes to be implemented in parallel and thus independently of cycle time. While insertion at the first station is manual, station two can be welded and station three can be checked and removed."
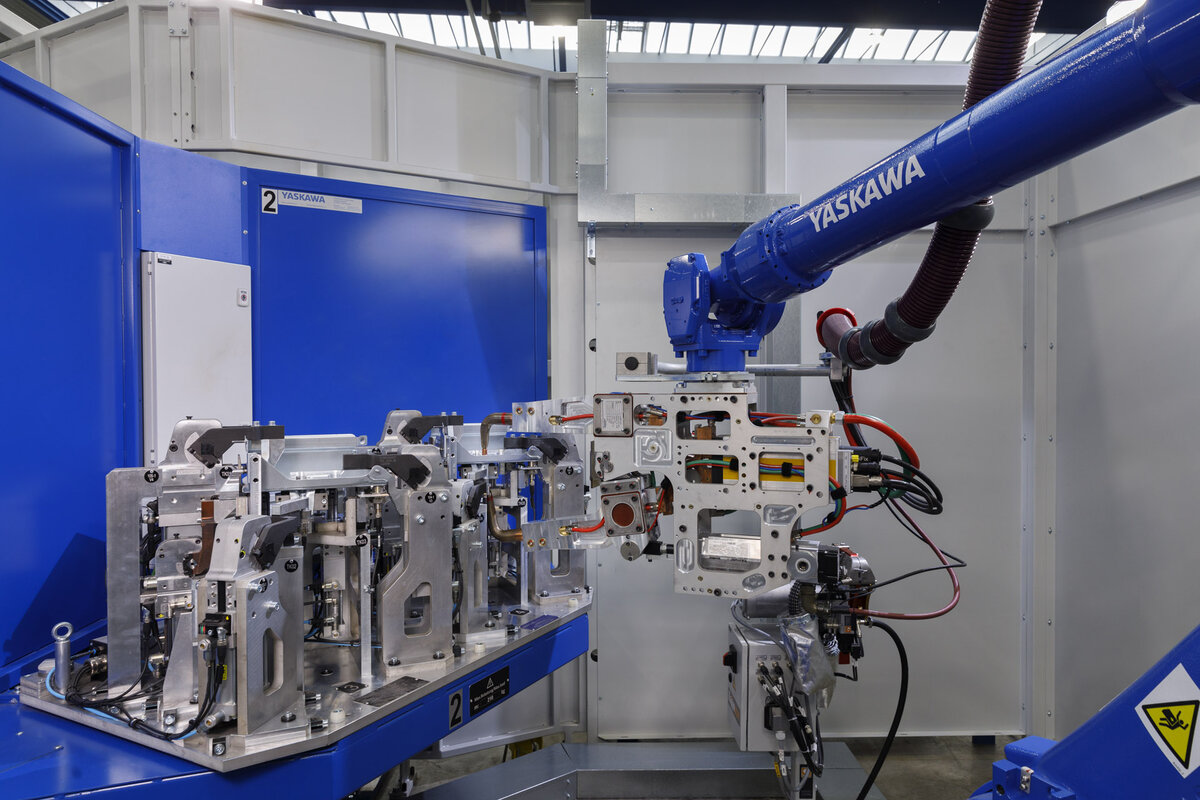
Picture: The Yaskawa GP88 is equipped with a complex double gripper for handling tasks.
Well-conceived solution with convincing details
The recently commissioned system convinces with many well-conceived details and very tight space requirements. It goes without saying that each component was selected with highest performance and reliability in mind.
Starting with the robots: a slim Motoman six-axis high-performance SP series assumes the task of spot welding, while a fast and equally precise GP88 is responsible for the handling processes. Thomas Pflüger: “There was no great need for discussion when selecting the robots. We are already using several Yaskawa robots and know that the “Motoman robots” will meet our requirements one hundred percent. They are highly reliable endurance runners that master every production marathon with flying colours.”
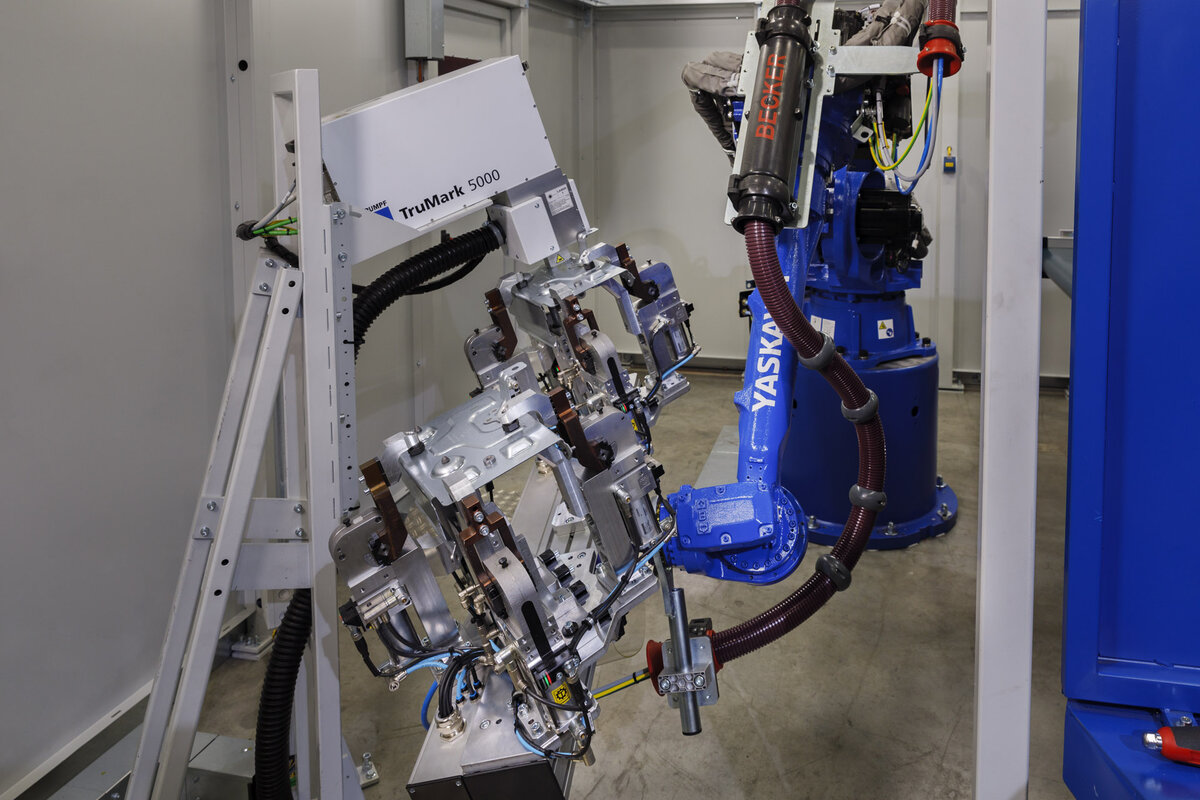
Picture: Complex issue - the GP88 with two components in the gripper for laser signing.
Designed for maximum availability
Thanks to their quality, all other components should also ensure high availability. In use are, among others, a servo-welding gun in lightweight construction, an automatic cleaning and change station for the electrode caps, a 2D camera system from Cognex for quality assurance, a Class 1 marking laser from Trumpf, a Siemens PLC and, of course, a state-of-the-art welding control system from Bosch Rexroth with permanent monitoring of the welding parameters.
A highlight of the system is the 3-station vertical positioner, which is equipped with two fixture nests per station, for parallel processing of six battery frames. Roland Hermann: “What makes it special is that this solution is based on a standard Yaskawa product, the R-1000 positioner, which has a vertical axis of rotation. We provided this modular basic drive with a base plate designed for automatic devices and executed the three-station solution. The 120 degree rotation required for the application is implemented in operation purely by software. The positioning axis is integrated into the robot master control system as a fully-fledged robot axis.”
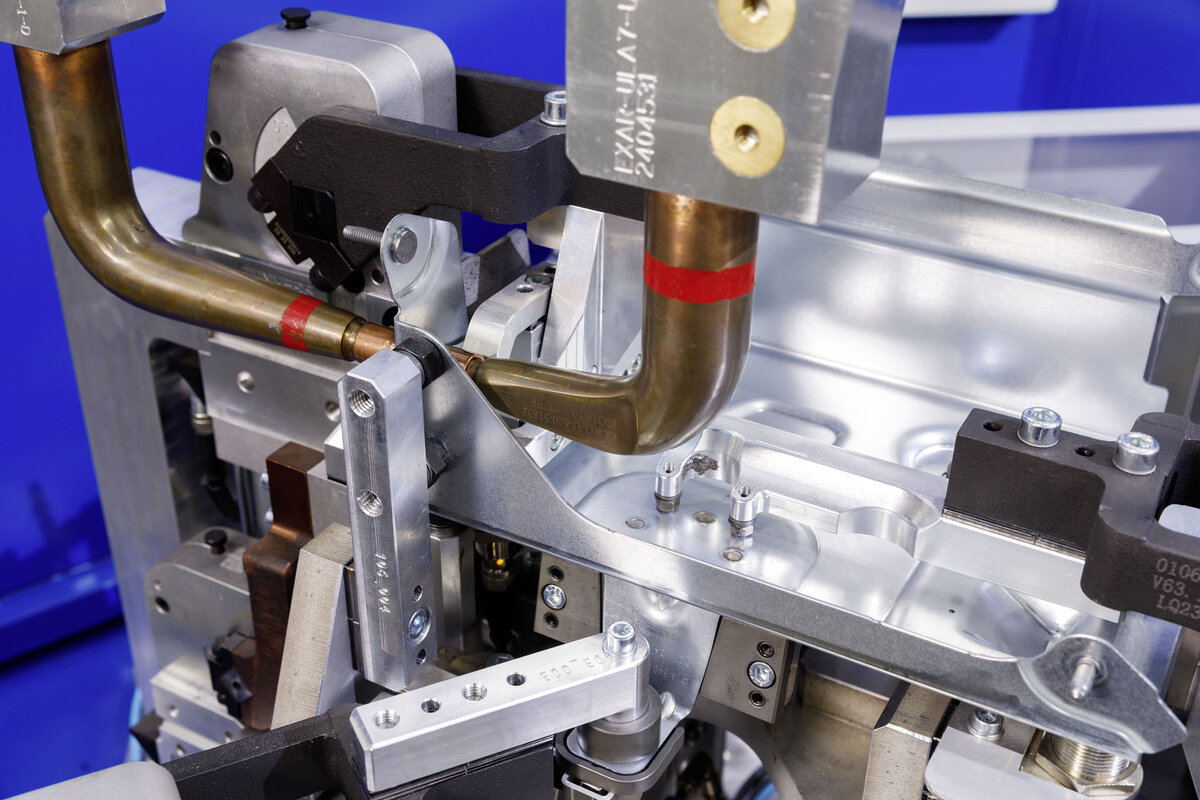
Picture: The weld points are sometimes difficult to access, but the programmers have done an excellent job.
Determines the cycle time: cleaning and replacement of electrode caps
The state of the electrode caps is, of course, decisive for the process. The regular cleaning of the caps by milling off the resulting zinc layer and replacement after a specific number of milling operations are fully automatic at the station, without the operator’s intervention. Since this process is one of the cycle time-determining processes, the positioning of the cleaning and change station was selected to ensure the shortest travel distances of the robot.
Once the spot welding is completed, the positioner continues to cycle again by 120 degrees to station three. Here – still in the fixture – the presence and correct fit of threaded pins and a nut are checked by camera. After successful QS testing, the slim Motoman GP88 with its pneumatic double gripper simultaneously removes both components and proceeds to the laser marking station, where the components receive a number-letter code that serves for identification and part traceability.
Special additional laser protection devices could be dispensed with when implementing the signing, as the components are guided by the handling robot to the marking head in a laser-safe manner. This is achieved by applying predefined pressure from the robot to the sealing elements of the marking head, thus implementing the requirements for laser safety. In the last step, the six-axis robot deposits the OK parts on a conveyor belt that is manually unloaded. Components determined not to be OK by the camera or the welding control system are placed by the handling robot in a separate box monitored for quantity.
The overall control of the system is implemented by a higher-level Siemens S7 PLC with visualization, to which the two robot controllers Yaskawa YRC 1000 are connected via Profinet. Since commissioning the system has run smoothly on both the software and hardware side. The decision in favour of Yaskawa has never been regretted at Binder.
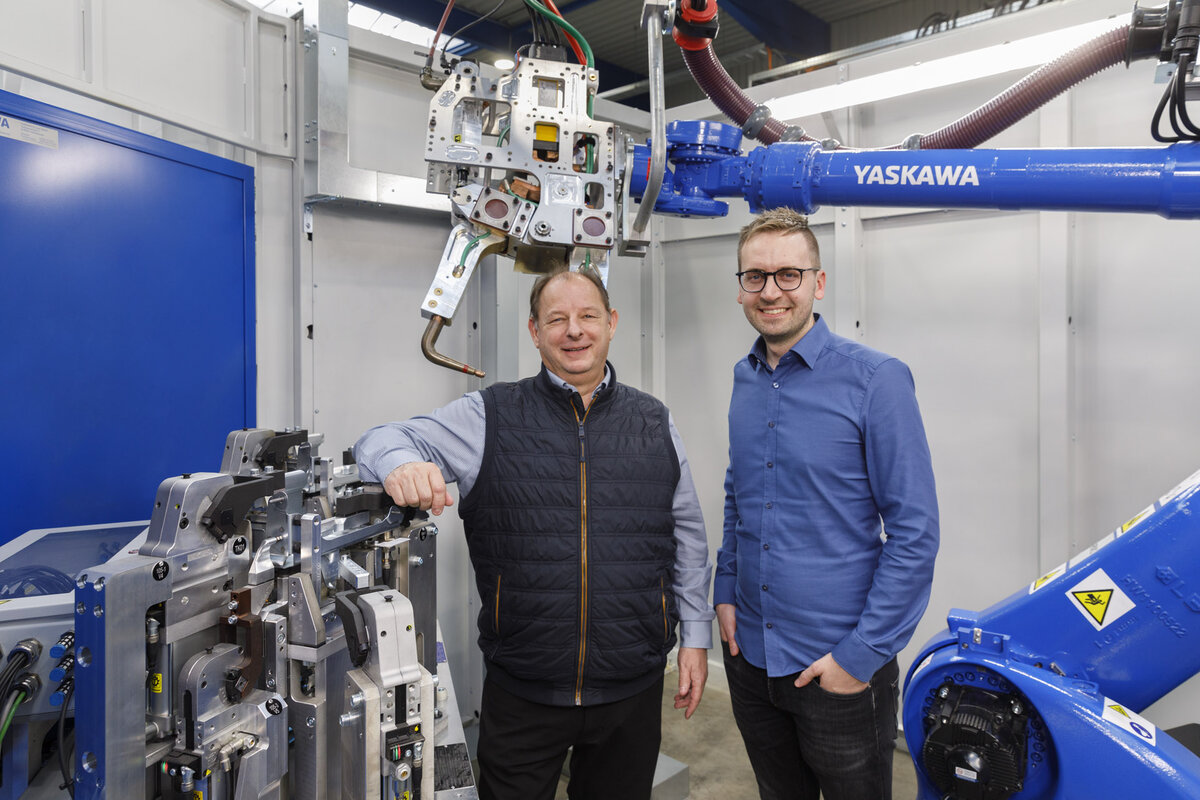
Picture: Roland Hermann (left), Yaskawa and Thomas Pflüger, Gebr. Binder are delighted about the successfully completed project.
Text: Ralf Högel
Pictures: YASKAWA Europe GmbH